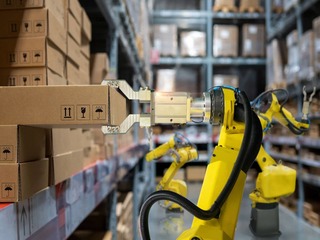
The company driving AGV/AMR technology
Noovelia's robots are flexible and vertical agnostic, automating the entire engineering process
In the early 20th century, Henry Ford made one of the first automations in manufacturing with a mechanical belt that drove production up sixfold. A century later, these automated machines, now called robots, carry out half of total manufacturing work worldwide, and they’re just getting smarter and stronger.
There are many reasons why automation has spread so fast, not the least of which was the global pandemic that kept people at home, contributing to such labor shortages. In Canada, 200,000 manufacturing positions were unfilled, a number predicted to triple by 2030. Automation can also take over dangerous tasks that result in $171 billion a year in costs associated with disabling or non-fatal workplace injuries. From the point of view of the owner of the manufacturing plant or facility, automation makes a lot of financial sense, especially with the rise of AGVs and AMRs.
Automated guided vehicles (AGV) and autonomous mobile robots (AMR) can be used to transport dangerous and raw materials, as well as pick up heavy or hard to reach items, and then set them down. Instead of a worker needing to do these tasks, and potentially risk hurting themselves, they can focus on other things that need to be done.
“Automating logistics operations frees up resources so workers can be put into positions where they will add value,” said Stephan Elliott, co-founder and CEO of Noovelia, a company that creates AGV and AMR devices. “Right now, there are many open jobs for machine and assembly line operators that need to be filled in North America, and there’s also a lot of demand for forklift operators.”
AGVs vs AMRs
The main difference between AGV and AMR is where they’re able to go and how they’re operated: AMRs are like cars, so they can go anywhere, and AGVs are like trains, meaning they have to stay on a set path. That means AMRs can drive and maneuver around obstacles on their own, while AGVs have to stop if something blocks them.
The two devices also operate in different kinds of environments; since AMRs are more versatile, they can be used in a wider range of applications, such as being programmed to follow around a human and assist them with their tasks, while AGVs are designed for applications with simpler logistics, featuring unchanging routes that do not require adaptation.
These technologies are still fairly new, but they’re already being adopted fairly quickly: mobile robot shipments grew by 53% in 2022 and it's predicted that there will be four million mobile robots installed by the end of 2027, 1.5 million of which will be installed that year alone.
The Noovelia solution: flexibility
Noovelia’s mission is to automate the entire engineering process for the manufacturing industry to help overcome labor shortages with a solution that’s adaptable for each manufacturing plant and across different industries.
Elliot left his job as a maintenance engineer in the aluminum industry to pursue just that: a flexible solution. While there are a number of companies making AGV and AMR devices, there’s one thing that sets Noovelia apart: how customizable its vehicles are. It can change the dimensions of its vehicles to fit into its customer’s existing space, while its competitors, instead, force their customers to change the space to fit the vehicles, which is much more complicated and costly.
“A lot of our competitors say, ‘you want to implement our vehicle in your factory, you need to have this space, you need to have this area, and change your production plant or layout to be able to implement the vehicle.’ On our side, if you have some restrictions, we will adapt our product,” Elliot said.
"Our technology is unique because we always try to be in the use case where it's more difficult for our competitors to go. For example, we are more flexible, so if you want to change the dimension of the vehicle on our side it’s very, very, very easy. We can provide a vehicle that's four by six foot or we can provide a six by eight, it's not a problem for us and it’s a low-cost price. If you want to go to a very high capacity, we have some models that can go as high as 5,000 and 10,000 pounds; normally it's more around 1,500 or 2,000 pounds, but we do higher capacity.”
Dimension change is just one flexible aspect of Noovelia’s solution, but it's not the only one. Adaptable and flexible solutions are applied at multiple levels: autonomy, speed, connectivity, tooling, and more.
Smart robots
The company will also provide required connectivity (REST API for example - REST is an architecture used to exchange information) so that autonomous vehicles can communicate in real time with other systems and ensure that everything functions properly. Noovelia calls itself a “one-stop-shop” by providing custom machinery and special components.
“We don't provide a product, we provide a solution, and we always try to follow our customer. Providing support is very important. The history of AGVs across the industry is a nightmare, with customers buying vehicles, trying to implement them in their factory and then, after a couple of months, putting them on the side and going back to the old tech technology,” explained Elliot, adding, “It is important to understand the process, the client's reality. Autonomous vehicles are part of a whole. You have to make sure you understand all the subtleties of the production flow so the solution is perfectly integrated into the process, all in a transparent manner.”
For example, Noovelia’s system also uses RFID (radio frequency identification) technology to direct robots to the right area in a warehouse. This happens without human workers involved. There’s also printed labels with embedded chips that identify the actual product that’s being transported and is recorded in a database.
One of Noovelia’s customers is Canadel, a furniture company that has been assembling and finishing their products by hand for more than 40 years..The company has six factories and 650 total employees, with its chair factory being the largest, employing 200 workers across multiple departments for silk upholstery, fabric cutting, and production.
The company’s main challenge was to be able to assign all the chairs in order to transport them to the right department; previously, everything was done by humans but a labor shortage, along with an expansion of their factory, meant they needed a solution that would optimize production and allow employees to work on the products instead of having to transport them.
Noovelia’s AGVs, which are directed by RFID instructions, can drive chairs to the right department without the need for human intervention, while printed labels with embedded chips identify the product so the database can recognize what operations need to be performed on that chair model, and the route is transmitted directly to the AGV.
Vertical agnostic
Currently, Noovelia has between 300 or 400 units in operation, and the company is vertical agnostic, meaning it can be used in any type of facility that needs to streamline tasks such as product movement, supplying assembly stations with parts/raw materials, palletizers, and packaging machines towards warehouses.
“Some of our customers have a lot of AMR and a lot of automation in their plant already, and other ones don’t have any but our business is increasing at an exponential speed right now because these companies see Amazon and a lot of very, very large companies implementing them so now even the smallest company is saying, ‘okay, it's for me too,’” said Elliot.
The company’s customers include a variety of customers across multiple industries, including commercial and industrial HVAC, furniture, data centers, agriculture and large part inspection with robots, and much more.
Conclusion
With manufacturing companies facing all sorts of challenges and headwinds, from labor shortages to disrupted supply chains, they are increasingly turning to automation to help streamline operations and to save money.
That’s where AGV and AMR come in; while they’re among the newest technologies being implemented, they’re growing fast. Using artificial intelligence and machine learning to do the types of repetitive, and sometimes dangerous, tasks that a human doesn’t need to do.
“The possibilities with this technology are amazing and it’s growing so fast. With the trend of industry 4.0, AI, collaborative robotics, the possibilities are endless. It's amazing,” said Elliot.
"Noovelia will change the way AVGs and AMRs are seen, change the way the implementation works so that the customer does not need to change their entire operations, layout, or plan to include AMR in the business. We want to be very flexible, modular, not necessarily the lowest cost, but the best return on investment. With our scaling plan, we want to be one of the master players in the modular and adaptation AGV and AMR space in North America."
Related News
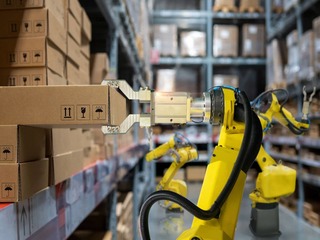